In today’s fast-paced and highly competitive market, the manufacturing industry is under constant pressure to innovate and adapt. One of the most significant advancements that have revolutionized this sector is the implementation of Enterprise Resource Planning (ERP) systems in the manufacturing industry. Even with ERP in small-scale manufacturing. By combining cutting-edge technology with streamlined processes, these systems have become a game-changer for most manufacturers worldwide.
ERP systems act as a central computer system for manufacturing operations, providing real-time visibility and control over various aspects of the business, including real-time inventory control, production planning, and delivery. With the ability to integrate different departments and functions within an organization, ERP systems streamline operations, eliminate inefficiencies, and drive growth.
The benefits of ERP systems in the manufacturing industry are many. Manufacturers can leverage accurate and up-to-date data to make informed decisions, enhance collaboration among teams, improve customer satisfaction, and reduce costs. With greater visibility into the entire manufacturing process, companies can optimize resource utilization, identify bottlenecks, and streamline workflows.
In this article, we will explore how ERP systems are transforming the manufacturing industry, empowering businesses to stay ahead in an increasingly competitive landscape. From small-scale manufacturers to large corporations, how the adoption of cloud-based ERP for manufacturing is driving growth and propelling the industry towards a more efficient and profitable future.
Understanding ERP systems in the manufacturing industry
In the dynamic and competitive landscape of the manufacturing industry, the need for efficient and integrated business management solutions has never been more crucial. Enter Enterprise Resource Planning (ERP) systems – the technological backbone that is transforming the way manufacturers operate.
ERP systems are comprehensive software platforms that integrate and automate various business functions, including production planning, inventory management, financial accounting, human resources, and customer relationship management. These systems serve as a centralized database for all critical data, enabling manufacturers to streamline operations, enhance decision-making, and drive overall business performance.
At the core of an ERP system’s functionality lies the ability to integrate disparate departments and processes, breaking down the traditional silos that often hinder efficiency and communication. By providing a single, unified view of the organization, ERP systems empower manufacturers to make informed decisions based on real-time data, optimize resource utilization, and respond quickly to changing market demands.
The benefits of implementing an ERP system in manufacturing
Implementing an ERP system in the manufacturing industry can unlock benefits that contribute to enhanced operational efficiency, improved financial performance, and sustained competitive advantage.
One of the primary advantages of ERP systems is the ability to improve inventory management. By providing real-time visibility into stock levels, production schedules, and supply chain activities, manufacturers can better forecast demand, minimize excess inventory, and reduce the risk of stock-outs. This optimization of inventory levels not only frees up valuable capital but also streamlines the overall production process.
Another key benefit of ERP systems is the enhancement of production planning and scheduling. These systems use data and resources available, to create a comprehensive production plan. This enables manufacturers to identify and address bottlenecks, optimize workflow, and ensure on-time delivery of products, ultimately improving customer satisfaction. Before the production starts.
Furthermore, ERP systems facilitate improved financial management and reporting. By centralizing financial data and simplifying accounting processes, manufacturers can gain real-time visibility into their financial performance, streamline invoicing and billing, and make more informed decisions regarding budgeting, cost control, and profitability analysis. This level of financial transparency is crucial for maintaining a healthy and sustainable business.
For free implementation checklist or guides in PDF by us check this link
Case study showcasing successful implementation of ERP system in manufacturing
To illustrate the transformative impact of ERP systems in the manufacturing industry, let’s explore a case study of Pek Automotive d.o.o. in Slovenia that have successfully implemented the modular R-Wave ERP solution.
Pek Automotive d.o.o is a discrete robot manufacturing company, a mid-sized producer of agricultural automation with robotics. Prior to implementing an ERP system, the company faced challenges with complexify of different software systems, paper based production processes and expensive consultants. By deploying R-Wave fully integrated cloud ERP Platform, the company was able to have all production systems in one place, streamline it’s operations, and gain real-time visibility into it’s business. In addition to improving and innovating the manufacturing process and eliminate paper usage.
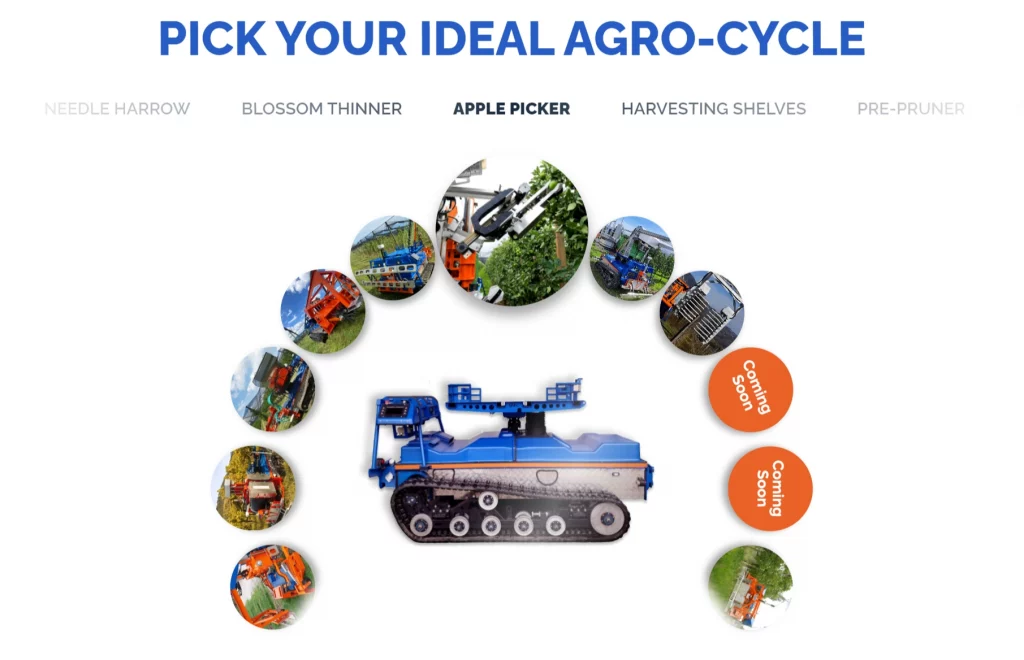
See more information on https://pekauto.com/ or https://promo.slopehelper.com/
Click here to read about Special Purpose Vehicle Manufacturing.
Key features and functionalities of ERP systems for manufacturing operations
ERP systems for the manufacturing industry are designed to address a wide range of operational needs, encompassing various features and functionalities that enable manufacturers to optimize their processes and drive growth.
One of the core capabilities of ERP solutions for discrete manufacturing is production planning and scheduling. These systems integrate data to create a comprehensive production plan. This allows manufacturers to identify and address potential bottlenecks, optimize workflow, and ensure on-time delivery of products.
Another critical feature of ERP systems is inventory management. These systems provide real-time visibility into stock levels, materials, and finished goods, enabling manufacturers to better forecast demand, minimize excess inventory, and streamline the procurement and replenishment processes. This optimization of inventory levels not only frees up valuable capital but also improves overall operational efficiency.
ERP systems also play a crucial role in quality control. By integrating quality assurance processes, tracking product specifications, and managing requirements, these systems help manufacturers maintain high-quality standards, reduce the risk of defects, and ensure compliance. This, in turn, enhances customer satisfaction and reduces the potential for costly recalls or other problems.
Choosing the right ERP system for your manufacturing business
Selecting the appropriate ERP system for a manufacturing business is a critical decision that requires careful consideration of various factors. As manufacturers navigate the diverse ERP landscape, it is essential to evaluate their unique business requirements, operational complexities, and long-term strategic goals.
One of the primary considerations in choosing an ERP system is the level of industry-specific functionality and configuration. Manufacturing businesses often have specialized needs, such as advanced production planning, quality control, and supply chain management. Selecting an ERP system that is tailored to the manufacturing industry and can be readily configured to meet these specific requirements is crucial for ensuring a seamless integration and maximum operational efficiency.
Another important factor is the scalability and flexibility of the ERP system. As manufacturing businesses grow and evolve, their technology needs may change. An ERP system that can easily accommodate changes in production volumes, product lines, or organizational structures will enable manufacturers to adapt to market demands and stay ahead of the competition.
The capabilities of the ERP system as standalone or in combination with other software are also a critical consideration. Manufacturers often rely on a wide range of specialized software and systems, such as Computer-Aided Design (CAD), Manufacturing Execution Systems (MES), and Supply Chain Management (SCM) tools. Selecting an ERP system that can be used with these systems or on the side can enhance data flow, improve decision-making, and streamline overall operations.
Additionally, factors such as user-friendliness, accessibility, and the availability of comprehensive training, documentation and support should be evaluated to ensure a smooth implementation and adoption process within the organization.
Implementing an ERP system in the manufacturing industry – challenges and best practices
While the benefits of implementing an ERP system in the manufacturing industry are well-documented, the process of successful implementation is not without its challenges. Navigating these challenges and adopting best practices is crucial for ensuring a seamless transition and maximizing the value of the ERP investment.
One of the primary challenges in ERP implementation is the complexity of integrating separate systems and processes if the ERP system is not “out of the box” or already fully integrated. Manufacturers often have a diverse range of legacy systems, each with its own data structures and workflows. Effectively consolidating and harmonizing these systems within the ERP framework can be a big task, requiring careful planning, data migration, and change management strategies.
Another common challenge is the resistance to change within the organization. Managers or employees may be hesitant to adapt to new processes and technologies, leading to potential adoption barriers and delays in realizing the full benefits of the ERP system. Addressing this challenge requires a comprehensive change management approach, including effective communication, comprehensive training, and the active involvement of key stakeholders throughout the implementation process. With a positive end goal in mind and the benefits of adopting to a new system.
Ensuring data accuracy and integrity is also a critical concern during ERP implementation for manufacturing. Manufacturers must meticulously clean and migrate data from existing systems to the new ERP platform, as inaccurate or incomplete data can undermine the effectiveness of the system and lead to poor decision-making.
To overcome these challenges and ensure a successful ERP implementation, manufacturers should adopt best practices such as:
- Conducting a thorough assessment of current business processes and pain points to align the ERP system with the organization’s specific needs.
- Involving key stakeholders, including cross-functional teams and end-users, throughout the implementation process to foster buy-in and facilitate a positive change within management.
- Developing a detailed implementation plan that outlines clear timelines, milestones, and resource allocation.
- Providing extensive training and ongoing support to employees to ensure seamless adoption and utilization of the new ERP system.
- Continuously monitoring and optimizing the ERP system to adapt to evolving business requirements and take advantage of new functionalities.
By embracing these best practices and proactively addressing the challenges inherent in ERP implementation, manufacturers can pave the way for a successful and sustainable ERP adoption, ultimately driving operational excellence and long-term growth.
How ERP systems streamline manufacturing operations and improve efficiency
At the heart of the transformative impact of ERP systems in the manufacturing industry lies their ability to streamline operations and drive efficiency across various business functions. By integrating and automating key processes, these systems enable manufacturers to optimize resource utilization and strengthens the company’s reputation in the market.
By centralizing financial data and automating accounting processes, these systems help manufacturers optimize resource allocation, identify cost-saving opportunities, and improve overall financial health. This, in turn, leads to cost savings, improved customer satisfaction, and increased competitiveness in the market. This is how to choose the right ERP for a manufacturing company, by finding the right match for your company goals.
The role of ERP systems in driving growth and profitability in the manufacturing industry
The implementation of ERP systems in the manufacturing industry has not only streamlined operations and improved efficiency but has also played a pivotal role in driving growth and profitability for businesses. By leveraging the capabilities of these software platforms, manufacturers can unlock a wide range of strategic advantages that contribute to long-term success and sustainable competitive edge.
One of the key ways to get ERP software benefits is drive growth is by enhancing customer satisfaction and loyalty. By providing real-time visibility into inventory levels, production schedules, and delivery timelines, manufacturers can better meet customer demands, reduce lead times, and improve on-time delivery. This, in turn, leads to higher customer satisfaction, increased repeat business, and the potential for new customer acquisition.
Moreover, the data-driven insights provided by manufacturing ERP solutions is to enable manufacturers to make more informed decisions regarding product development, pricing, and market expansion. By analyzing sales trends, production data, and financial performance, manufacturers can identify new opportunities, allocate resources more effectively, and develop innovative products that cater to evolving market needs. This data-driven decision-making process is crucial for driving growth and market share expansion.
Furthermore, the adoption of ERP systems with other enterprise-wide technologies, such as supply chain management, customer relationship management, and business intelligence tools, enables manufacturers to achieve greater operational visibility and cross-functional collaboration. This holistic approach to business management allows manufacturers to identify and capitalize on synergies, drive organizational alignment, and unlock new avenues for growth and profitability.
By leveraging the transformative capabilities of ERP systems, manufacturers can not only streamline their operations and improve efficiency but also position themselves for long-term growth and sustainable profitability. As the manufacturing industry continues to evolve, the strategic importance of ERP systems will only continue to increase, making them a crucial investment for businesses seeking to stay ahead in an increasingly competitive landscape.
Training and support for implementing and using ERP systems in manufacturing
Successful implementation and ongoing utilization of ERP systems in the manufacturing industry require a comprehensive approach to training and support. Ensuring that employees at all levels understand the system’s functionality, can effectively navigate its features, and are equipped to adapt to the new processes is essential for unlocking the full potential of the ERP investment.
One of the critical components of effective ERP training is the development of comprehensive training programs tailored to the specific needs and roles of different stakeholders within the organization. This may include role-specific training for production managers, inventory specialists, finance professionals, and end-users, ensuring that each group is equipped with the knowledge and skills necessary to leverage the ERP system to its fullest extent.
In addition to formal training sessions, manufacturers should also consider implementing ongoing support mechanisms, such as helpdesk services, user manuals, resources and online tutorials. These resources can help employees troubleshoot issues, access relevant information, and continuously enhance how ERP improves efficiency in manufacturing.
Effective change management is another crucial aspect of ERP implementation and support. Manufacturers should proactively address resistance to change by engaging employees, communicating the benefits of the new system, and emphasizing the importance of their roles in the transition. This can be achieved through interactive training sessions, regular feedback loops, and the identification of ERP champions within the organization who can serve as advocates and mentors for their colleagues.
Furthermore, manufacturers should consider investing in ongoing system maintenance and upgrades to ensure that cloud ERP for manufacturers remains up-to-date and aligned with evolving business requirements. This may involve partnering with the ERP vendor or engaging with specialized IT support services to provide regular system updates, address any technical issues, and explore new functionalities that can further enhance operational efficiency and growth.
By prioritizing comprehensive training, ongoing support, and proactive change management, manufacturers can ensure that their ERP investment yields maximum benefits, empowering employees to fully leverage the system’s capabilities and drive continuous improvement across the organization.
Conclusion: The future of ERP systems in the manufacturing industry
As the manufacturing industry continues to evolve, the role of Enterprise Resource Planning (ERP) systems in driving operational excellence, enhancing competitiveness, and fueling growth will only become more crucial. These integrated software platforms have already transformed the way manufacturers operate, and their influence is poised to expand even further in the years to come.
The future of ERP systems in the manufacturing industry is marked by several key trends and developments. Firstly, the increasing adoption of cloud-based ERP solutions is set to revolutionize the way manufacturers access and utilize these systems. Benefits of real-time data in manufacturing ERP systems is by leveraging the scalability, flexibility, and cost-effectiveness of cloud technology. Manufacturers can more easily adapt to changing business requirements, access the latest features and functionalities, and streamline their IT infrastructure.
Furthermore, the integration of ERP systems with other enterprise-wide technologies, such as supply chain management, customer relationship management, and business intelligence tools, will continue to evolve, enabling manufacturers to achieve greater operational visibility, cross-functional collaboration, and strategic decision-making capabilities.
As the ERP solutions for discrete and process manufacturing navigates the challenges of globalization, technological disruption, and changing customer preferences, therefore the role of ERP systems will become increasingly more important in the future.
If you want to read more about us and our solution, please check out our homesite here or get a free demo version you can test out yourself here.